In the early 2000s, several NGO reports drew attention to harsh working conditions at a factory in Honduras producing for Gildan, the Montreal-based company. This article explores the important advancements that have been made since then, in particular concerning the safety of workers.
While issues of respect for union rights and freedom of association are still a concern, the more open dialogue between unions, NGOs and the company in recent years has allowed workers to have their problems addressed in a more timely and effective manner.
Founded in 1984, Gildan went from being a small company on the brink of bankruptcy in the 1990s to one of Canada’s top t-shirt manufacturers, with a net income of US 259.8 million dollars in 2019. The company is even able to compete with Asian manufacturers, a rare accomplishment for a western company in the textile industry.
Gildan mainly achieved this by outsourcing its production to countries with low minimum wages such as Honduras and Haiti. The company claims that the choice of location for these facilities involves many factors such as the presence of a qualified workforce, production in the Western Hemisphere allowing close proximity to main markets and the ability to leverage free trade agreements, which are competitive advantages that allow Gildan to compete against Asian imports with poor CSR standards.
Labour rights violations at Gildan in the 2000s
Gildan’s factory in El Progreso, Honduras employed about 1,800 workers. It is in this factory that complaints were most frequent, starting in 2001 when workers accused the company of violating several labour rights. These drew the attention of the Maquila Solidarity Network (MSN), a Toronto NGO focused on improving the condition of workers in the textile industry.
Along with other NGOs, MSN conducted an inquiry and released a joint report about the situation in 2003, identifying several serious issues.
Workers complained about repetitive strain and wrist injuries. There were occasions when workers lost fingers using machines with blades. According to the employees, these injuries were due to the intense work pressure; workers at the plant sometimes worked eleven-hour shifts and had to meet daily production targets that varied.
Female workers under temporary contracts claimed that they had to take mandatory pregnancy tests, and that if the results were positive, they were fired without compensation. The MSN reported that Gildan responded to these allegations by stating that it performed drug tests (not pregnancy tests) to comply with its Code of Conduct and to ensure that shipments were drug free.
The MSN report also stated that several workers were fired for trying to join a union, thus violating Honduran labour laws.
Another report was issued a year later by the Fair Labour Association (FLA), a collective effort of businesses, civil society organization and universities aiming to promote compliance to international labour laws. Gildan is one of the FLA’s participating companies and agreed to the association’s code of conduct, but the FLA report outlined several breaches of those standards, coming to the same conclusions as the MSN.
Gildan’s corporate social responsibility program
To better understand the aftermath of the scandals, I interviewed two members of the FLA, Eric Biel, a senior advisor who previously worked as a managing director for corporate social responsibility in the private sector, and Jessica Vasquez, the association’s CSO Engagement Manager.
According to Biel, the MSN and FLA reports in the early 2000s had significant impacts on the company. “Gildan was brought under what was called a 90-day review process that went all the way up to the board level and was even at some risk of being expelled from the FLA. It therefore had to implement a Corrective Action Plan in order to keep its accreditation from the organization.”
In August, 2004 Gildan closed the factory, and in 2005 submitted its plan to the FLA. The MSN suspended its campaign.
Gildan undertook deep changes to improve its image, for example creating its “Genuine Responsibility Program” in 2004. Jessica Vasquez says that, “Gildan has provided valuable insights on their experience in Honduras and their advancements on specific issues such as childcare, health and safety at the workplace.”
However, Eric Biel advices caution when evaluating a company’s respect for labour rights through a company’s CSR program, as some companies use such programs primarily to enhance its public image.
“For any company that talks about its CSR program, you have to examine the particulars,” he said. “Are its commitments ones that it’s working on its own? Is it working in connection with non-governmental organisations when it comes to labour standards or important environmental organisations when it comes to sustainability criteria? Does it have transparent reporting?”
In fact, the 2018 CSR report from Gildan outlines several important improvements, in particular regarding worker safety. Over the past ten years the rate of work-related injury has de-creased by 50% and their severity rate by 67%. Moreover, 96% of Gildan employees are represented by formal health and safety committees and 77% of its facilities have free on-site health clinics open 24/7. Several facilities also offer childcare workshops to pregnant workers as well as free counselling sessions. In 2018, over 50% of Gildan’s workforce worldwide was covered by a collective bargaining agreement.
Gildan claims that it has invested more than US$13.6 million in supplemental benefits, such as subsidized meals, free transportation, vaccines, medicine and vitamins, for many of its 50,000 workers worldwide.
Gildan takes a lot of pride in its program in Honduras, pointing to the awards and recognition it has received, like the Foundation of Corporate Social Responsibility in Honduras (FUNDHARSE) seal, most recently in September 2019, which recognizes companies that demonstrate leading practices related to corporate social responsibility. Gildan has engaged in supporting sustainable production and consumption, healthcare and recreational facilities in the country. Through its “Young Sustainability Leaders” program, Gildan also works with World Vision in some schools “to inspire and empower students to be the next generation of social and environmental entrepreneurs.”
Imperfect progress – El Progreso in 2019
Gildan purchased Anvil Knitwear and related manufacturing facilities in May 2012. As part of this acquisition, the company acquired STAR, a unionized sewing facility located in Honduras. In recent years, the SITRASTAR union at the STAR factory filed complaints claiming that management was firing workers on the basis of their involvement in the union and threatening workers with termination if they tried to join it.
In July 2019, Gildan made the decision to close the STAR plant. Several factory workers claimed that Gildan was closing the factory in order to dismantle the SITRASTAR union. According to Gildan, the STAR facility was closed in order to benefit from the unused production capacity at two larger sewing plants.
In an e-mail, Geneviève Gosselin, Director of Corporate Communications & Marketing at Gildan, stated that STAR workers have received benefits from the company to cope with the closure.
“All of the workers at STAR have been provided a severance package that goes beyond the minimum requirements under Honduran law,” Gosselin wrote. “100% of the workers have been offered to be rehired at the two other sewing facilities where the production is being moved. Both of these facilities are unionized and employees are covered under collective bargaining agreements.”
Once again the FLA investigated on the case, publishing its report in August 2019. While Gildan’s guarantees of severance packages and reemployments have indeed been implemented, the report indicates that the management violated Honduran labour laws and the FLA’s code of conduct during the closure of the factory. The company asserts that it engaged with labour authorities from the beginning of the factory closure, and that most of the time a labour inspector witnessed the termination process and all activities related to the closure.
According to Honduran law, a company has to request the authorization of the Ministry of Labour before closing a factory, which Gildan did not do. The company argues that the Honduras Labor Code does not provide specific guidelines related to this.
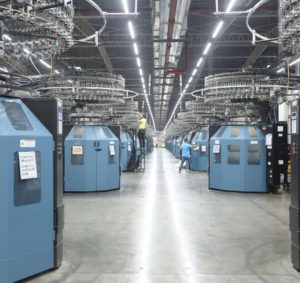
The company unilaterally terminated the collective bargaining agreement that was valid until 2021, and dismissed the union executive’s committee even though their term had not finished. The FLA code of conduct states that employers have to discuss alternatives to plant closures with the unions; the union was not consulted when the management decided to close the facility.
Many of the re-employed workers interviewed by the FLA investigators said that they did not receive information about what is being negotiated by their new unions, and did not know their union representatives or the content of the new collective bargaining agreement.
While it appears that there is still progress to be made regarding industrial relations, Gildan’s treatment of workers in Central America has improved in comparison to the scandals of the early 2000s.
“In Central America, there has been quite a lot of progress,” Jessica Vasquez says. “Gildan is, for example, part of the Americas Group, a multi-stakeholder initiative that includes NGOs, un-ions and brands. Through this initiative, they have provided valuable insights on their actions in Honduras, facilitated childcare for female employees and improved the safety of their workers.”
Jeffcott agrees that such initiatives are becoming more predominant in the garment industry, and reflect a democratization of the relationship between businesses, unions and NGOs.
“Years of work, with both labour rights groups and companies, can actually produce these positive results, where you have companies join in with labour organisations in support of reforms,” he says. “It doesn’t always result in huge changes. At least it opens the door to the organisations that represent workers, as they can talk directly to the brands and tell them what the problems are in the factories that produce for the brands.”